La porositat, discontinuïtats de tipus cavitat formades per atrapament de gas durant la solidificació, és un defecte comú però feixuc en la soldadura MIG i amb diverses causes.Pot aparèixer en aplicacions semiautomàtiques o robòtiques i requereix l'eliminació i la reelaboració en ambdós casos, cosa que comporta temps d'inactivitat i augment dels costos.
La principal causa de la porositat en la soldadura d'acer és el nitrogen (N2), que intervé en el grup de soldadura.Quan la piscina líquida es refreda, la solubilitat de N2 es redueix significativament i N2 surt de l'acer fos, formant bombolles (porus).En la soldadura galvanitzada/galvaneal, el zinc evaporat es pot agitar a la piscina de soldadura i, si no hi ha prou temps per escapar abans que la piscina es solidifiqui, forma porositat.Per a la soldadura d'alumini, tota la porositat és causada per l'hidrogen (H2), de la mateixa manera que funciona el N2 a l'acer.
La porositat de la soldadura pot aparèixer externament o internament (sovint anomenada porositat subsuperficial).També es pot desenvolupar en un sol punt de la soldadura o al llarg de tota la seva longitud, donant lloc a soldadures febles.
Saber identificar algunes causes clau de la porositat i com resoldre-les ràpidament pot ajudar a millorar la qualitat, la productivitat i els resultats.
Pobre cobertura de gas de protecció
La mala cobertura de gas de protecció és la causa més freqüent de porositat de la soldadura, ja que permet que els gasos atmosfèrics (N2 i H2) contaminin la piscina de soldadura.La manca de cobertura adequada es pot produir per diversos motius, inclosos, entre d'altres, un flux de gas de protecció deficient, fuites al canal de gas o massa flux d'aire a la cèl·lula de soldadura.Les velocitats de viatge massa ràpides també poden ser culpables.
Si un operador sospita que un flux deficient està causant el problema, proveu d'ajustar el mesurador de cabal de gas per assegurar-vos que la velocitat sigui adequada.Quan s'utilitza un mode de transferència d'esprai, per exemple, un flux de 35 a 50 peus cúbics per hora (cfh) hauria de ser suficient.La soldadura a amperatges més alts requereix un augment del cabal, però és important no ajustar-lo massa.Això pot provocar turbulències en alguns dissenys de canons que interrompen la cobertura del gas de protecció.
És important tenir en compte que les pistoles dissenyades de manera diferent tenen característiques de flux de gas diferents (vegeu dos exemples a continuació).El "punt dolç" del cabal de gas per al disseny superior és molt més gran que el del disseny inferior.Això és una cosa que un enginyer de soldadura ha de tenir en compte a l'hora de configurar la cèl·lula de soldadura.
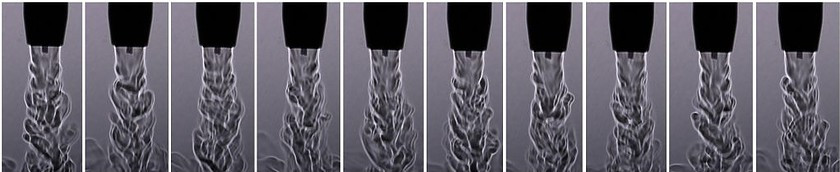
El disseny 1 mostra un flux de gas suau a la sortida del broquet
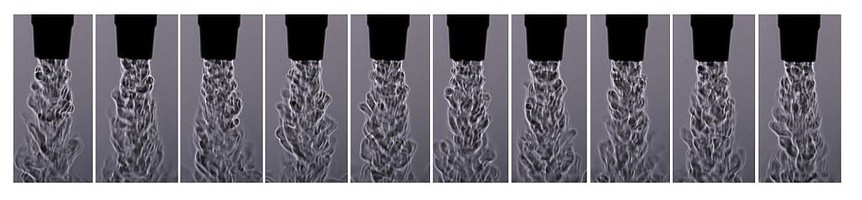
El disseny 2 mostra un flux de gas turbulent a la sortida del broquet.
Comproveu també si hi ha danys a la mànega de gas, els accessoris i els connectors, així com les anelles O al pin d'alimentació de la pistola de soldadura MIG.Substituïu segons sigui necessari.
Quan utilitzeu ventiladors per refredar operaris o peces en una cèl·lula de soldadura, tingueu cura que no s'apuntin directament a l'àrea de soldadura on puguin interrompre la cobertura de gas.Col·loqueu una pantalla a la cèl·lula de soldadura per protegir-la del flux d'aire extern.
Torneu a tocar el programa en aplicacions robòtiques per assegurar-vos que hi ha una distància adequada entre la punta i el treball, que normalment és de ½ a 3/4 de polzada, depenent de la longitud desitjada de l'arc.
Finalment, baixeu les velocitats de viatge si la porositat persisteix o consulteu un proveïdor de pistola MIG per a diferents components frontals amb una millor cobertura de gas
Contaminació per metalls base
La contaminació per metalls bàsics és una altra raó per la qual es produeix la porositat, des de l'oli i el greix fins a l'escala del molí i l'òxid.La humitat també pot afavorir aquesta discontinuïtat, especialment en la soldadura d'alumini.Aquests tipus de contaminants solen conduir a una porositat externa visible per a l'operador.L'acer galvanitzat és més propens a la porositat subterrània.
Per combatre la porositat externa, assegureu-vos de netejar a fons el material base abans de soldar i considereu l'ús d'un cable de soldadura amb nucli metàl·lic.Aquest tipus de filferro té nivells més alts de desoxidants que el filferro sòlid, de manera que és més tolerant a qualsevol contaminant restant al material base.Emmagatzemeu sempre aquests i qualsevol altre cable en una zona seca i neta de temperatura similar o lleugerament superior a la de la planta.Fer això ajudarà a minimitzar la condensació que podria introduir humitat a la piscina de soldadura i provocar porositat.No emmagatzemeu els cables en un magatzem fred o a l'aire lliure.
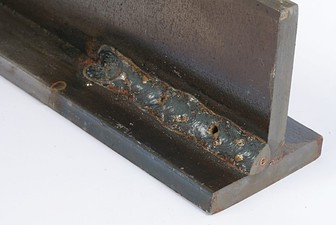
La porositat, discontinuïtats de tipus cavitat formades per atrapament de gas durant la solidificació, és un defecte comú però feixuc en la soldadura MIG i amb diverses causes.
Quan es solda acer galvanitzat, el zinc es vaporitza a una temperatura més baixa que l'acer fos, i les velocitats de desplaçament ràpides tendeixen a fer que la piscina de soldadura es congeli ràpidament.Això pot atrapar el vapor de zinc a l'acer, donant lloc a porositat.Combatre aquesta situació controlant les velocitats de viatge.Una vegada més, considereu un cable de nucli metàl·lic especialment dissenyat (fórmula de flux) que afavoreix l'escapament del vapor de zinc de la piscina de soldadura.
Broquets obstruïts i/o de mida inferior
Els broquets obstruïts i/o de mida insuficient també poden causar porositat.Les esquitxades de soldadura es poden acumular al broquet i a la superfície de la punta de contacte i el difusor, provocant un flux de gas de protecció restringit o fent que es torni turbulent.Ambdues situacions deixen la piscina de soldadura amb una protecció inadequada.
Per agreujar aquesta situació hi ha un broquet massa petit per a l'aplicació i més propens a una acumulació d'esquitxades més gran i ràpida.Els broquets més petits poden proporcionar un millor accés a les articulacions, però també obstrueixen el flux de gas a causa de la menor àrea de secció transversal permesa per al flux de gas.Tingueu sempre en compte la variable de la punta de contacte a l'enganxament (o rebaix), ja que aquest pot ser un altre factor que afecti el flux i la porositat del gas de protecció amb la vostra selecció de broquet.
Tenint això en compte, assegureu-vos que el broquet sigui prou gran per a l'aplicació.Normalment, les aplicacions amb un alt corrent de soldadura que utilitzen filferro de grans dimensions requereixen un broquet amb un forat més gran.
En aplicacions de soldadura semiautomàtica, comproveu periòdicament si hi ha esquitxades de soldadura al broquet i traieu-les amb unes pinces de soldadura (soldadores) o substituïu el broquet si cal.Durant aquesta inspecció, confirmeu que la punta de contacte està en bon estat i que el difusor de gas té ports de gas clars.Els operadors també poden utilitzar compostos anti-esquitxades, però han de tenir cura de no submergir el broquet dins del compost massa lluny o durant massa temps, ja que quantitats excessives del compost poden contaminar el gas protector i danyar l'aïllament del filtre.
En una operació de soldadura robòtica, invertiu en una estació de neteja de broquets o escariador per combatre l'acumulació d'esquitxades.Aquest perifèric neteja el broquet i el difusor durant les pauses rutinàries de producció perquè no afecti el temps de cicle.Les estacions de neteja de broquets estan pensades per funcionar juntament amb un polvoritzador antiesquitxades, que aplica una capa fina del compost als components frontals.Massa o massa poc líquid antiesquitxades pot donar lloc a una porositat addicional.Afegir una explosió d'aire a un procés de neteja de broquets també pot ajudar a eliminar les esquitxades soltes dels consumibles.
Manteniment de la qualitat i la productivitat
Tenint cura de controlar el procés de soldadura i conèixer les causes de la porositat, és relativament senzill implementar solucions.Fer-ho pot ajudar a garantir un major temps d'arc, resultats de qualitat i més peces bones que es mouen durant la producció.
Hora de publicació: 02-feb-2020